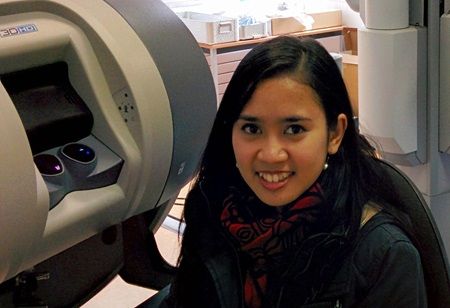
In an interaction with Asia Manufacturing Review, Dr Latifah Nurahmi, Assistant Professor at the Department of Mechanical Engineering, Institut Teknologi Sepuluh Nopember, Indonesia shares her views on the integration of friction stir welding robots into high-speed rail manufacturing workflows, the key focus areas and the challenges involved.
What are the specific mechanical and environmental conditions that a friction stir welding robot must be designed to handle in the high-speed rail manufacturing environment?
Let me describe the mechanical specifications of the robot that we are designing at the moment. Our team is developing a parallel manipulator with three translational degrees of freedom to accommodate a tool head for friction stir welding, especially for high-speed rail carriages. The robot must address two main mechanical factors: kinematics and dynamics. Kinematics requires accurate positioning of the tools to achieve the correct weld along the rail shapes. To assess the robot’s kinematic performance, we employ the Local Conditioning Index (LCI), which allows the tool to hold its position across the entire range of operations.
Dynamics concern the force application. In friction stir welding, a large amount of axial force is needed to plunge the tool and to produce enough frictional heat. The force must be applied constantly along the weld path and at the same time, the robot has to deal with considerable torque originating from the rotation of the tool. To measure the dynamic performance of the robot, we use the Dynamic Isotropy index which measures the robot’s behaviour in different positions. After dealing with these aspects, we progress to the path planning. To further enhance the tool speed, rotational speed, and force applied, we use a trapezoidal trajectory algorithm. This planning helps in developing the control scheme where we apply the computed torque control to make sure that the robot applies the right torque and offers the right forces for welding.
What are the limitations of current sensors and vision systems in monitoring and adjusting the welding process in real time, and how can these be addressed in the prototype design?
The limitations associated with sensors in friction stir welding are mainly due to the sensors themselves. For example, force and torque sensors have problems with low speed of response, and therefore the welding parameters adjustment is delayed. To overcome this, the use of high-speed data acquisition systems with faster processing capacity can help to minimize response time. Further, some of the sensors have low sensitivity which complicates the ability to capture small changes in the welding process. One can overcome this problem by using higher precision sensors that are sensitive over a broader range. In addition, due to high temperature in FSW and electromagnetic interference, the sensors used must be shielded to avoid the effect of heat and interferences hence avoiding calibration shift.
How can a prototype robot integrate with existing manufacturing workflows and automation systems, and what are the potential challenges in achieving seamless integration?
Multiple steps have to be followed when one wants to incorporate a friction stir welding robot into a manufacturing system. First of all, it is necessary to check the compatibility of the robot control system with the communication protocols of the manufacturing environment. There may be standardized procedures in the manufacturing systems while the robot may have its own. These protocols must be synchronized after the lab prototype development to ensure that data is exchanged efficiently during assembly. It is also important to design the robot with a modular architecture. This design also enables easy modification and subsequent growth to suit the requirements of friction stir welding. Modularity improves the robot’s flexibility since it can be designed to meet different needs within the manufacturing process.
Operator training is another important factor, which is frequently overlooked. Some of the key areas that should be included in the training include the operation of the robot and maintenance since the latter is as complex as the manufacturing system. This means that the management should be involved in this training process so that to ensure that the right resources are directed toward it. There may be issues with protocols, which are not compatible with the new system, or the current system may be obsolete. To overcome these, a custom interface developed in our lab can help to reduce the compatibility gap. Moreover, the issues of security and safety must be solved with the help of effective cybersecurity strategies. Lack of space in the factory may also call for a small robot size and the use of modularity to maximize the space used.
What are the cost implications of developing and deploying a robot for friction stir welding in high-speed rail manufacturing, and how can these be managed or minimized?
The costs that are associated with the development and implementation of a robot for friction stir welding in the manufacturing of high-speed railways are manifold. First, there are large costs during the design and building of a prototype, with testing on simple parts and then on scaled-up parts adding to the costs. Additional customization for particular welding processes also contributes to the high costs of development.
Actuators, sensors, controllers as well as welding tools that are at the core of the design make up a significant proportion of the budget in both development and implementation. System integration also incurs costs, as it needs to be integrated with other manufacturing systems, and this may need interfaces that may need to be developed in-house.
Maintenance, calibration, tool, actuator, and sensor checks are some of the factors that lead to the long-term cost. To control these costs, it is beneficial to begin with a pilot project. To ensure that the cost of the robot is determined, the robot is tested in a mini-environment for a certain period. Also, the use of standard components instead of the custom ones can greatly reduce the implementation expenses.
What are the potential safety and maintenance issues associated with the robot, and how can the design address these to ensure safe operation and ease of maintenance?
The issues of safety and maintenance in friction stir welding mostly relate to high temperatures and large welding forces. The tool has a high RPM and high force which is dangerous to the user. As opposed to conventional welding, robotic systems must be contained. To overcome these challenges protective enclosures should be designed in such a way that personnel is protected from heat and force. Proper insulation and the use of automated cooling systems should be employed to reduce the chances of touching hot surfaces. There should be clearly defined safety zones and restricted areas for the operators to avoid such mishaps. Moreover, there is a need for extensive training and awareness programs to avoid mishaps when operating or even interacting with the robot.